Several factors—from automation and big data to staffing shortages and culture shifts—will help guide the evolution of industrial maintenance.
These along with artificial intelligence,sensor technology, and budget constraints will become the standard in factories, pushing age-old reactive practices to the wayside. But how and why did equipment maintenance practices evolve from reactive to proactive? And what changes andtrendscan we expect to see in the future of maintenance?
What is industrial maintenance?
Industrial maintenanceis the service done by technicians or mechanics to manage machinery and equipment to increase uptime in order to meet the business objectives. It is used across multiple industries and can involve troubleshooting, fixing, and replacing equipment to improve asset performance.
What types of industrial maintenance are there?
Like any other aspect of industry and manufacturing, industrial maintenance — also called factory maintenance— is in a continuous state of development and enhancement. As experience and knowledge of industrial maintenance best practices have grown, so too has technology evolved, combining to create more effective ways of carrying our maintenance and managing equipment.
Types of maintenance — incorporating the full spectrum of development and evolution — include:
- Reactive maintenance:Reactive maintenance addresses maintenance needs for a machine or piece of equipment when a breakdown or obvious malfunction occurs. While reactive maintenance remains a necessary component of a maintenance plan, it is the most inefficient method of maintenance due to excessive unplanned downtime.
- Preventive maintenance:Preventive maintenance involves standard tasks designed to address typical, expected upkeep and maintenance needs during the lifecycle of a component or piece of equipment.Preventive maintenanceis a useful tool for avoiding preventable maintenance issues, but can also yield inefficiencies, such as investing resources in maintenance that is not required at that time.
- Predictive maintenance:Predictive maintenanceincorporates data and technology to provide insights about equipment performance and facilitate early alerts of potential maintenance issues. Predictive maintenance is driven by industrial sensor technology — including vibration sensors, ultrasonic sensors and thermographic sensors. It is a next step in the evolution of maintenance — thanks to the foresight, planning and efficiency that it yields.
- Reliability-centered maintenance:Reliability-centered maintenanceis the next step in the progression beyond predictive maintenance, using similar underlying sensor and data technology to enable a sharp focus on reducing unplanned downtime while increasing productivity. Reliability-centered maintenance incorporates remote monitoring, 24/7 systems and continuous data analysis to provide what is, today, the ultimate in decision-making data to keep machines operational while increasing capacity and fulfilling orders on time.
Industrial maintenance roles
Today’s industrial maintenance technology and methods call for a range of professional roles, including:
- Technicians:While sensors are generally easy to install and operate, technicians must be familiar and comfortable with the technology.
- Planners:Predictive maintenance and reliability-centered maintenance are most effective as part of a maintenance “ecosystem” — one where sensors are working in sync with one another to provide the most useful and actionable data for analysis. Planners are experts in developing and tailoring these ecosystems to yield the best results for you.
- Supervisors:Maintenance supervisors are involved in putting the pieces of technology- and sensor-driven maintenance together and making decisions based on the data and analysis at hand. This is a different process than reactive maintenance or standard scheduled, preventive maintenance.
- Engineering professionals:Engineering personnel are necessary for maintenance systems design, data analysis and more.
As technology becomes increasingly prevalent and necessary to maintain a competitive edge, capable personnel are a necessity. Combined with increased automation and streamlined operations, skilled workers andtechnical trainingprograms are more important than ever.
The history of industrial maintenance
Much has happened in manufacturing and maintenance practices since the industrial revolution, but the most dramatic evolution of maintenance has occurred in the last fifty years. These changes affected how industry plants have been maintained.
Before the Second World War, machinery was generally large, rugged and relatively slow running, with basic control systems and instrumentation. At this point in the history of maintenance, the demands of production were not as severe as they are today, so downtime was not as critical of an issue. When downtime did occur, it was addressed—but generally, these machines were reliable. In some older factories, machines manufactured in that period are still as good today as the day they were made.
战争结束后,下一阶段的设备维护ance history began — the rebuilding of industry. A much more competitive marketplace developed, forcing manufacturers to increase production. The overwork of machines leads to an increase in downtime and a rise in costs to fix machines. This increase in production demanded better maintenance practices, which lead to a key step in the evolution of manufacturing industry standards — the development ofpreventive maintenance.
Since the 1980s, plants and systems have become even more complex. The demands of the competitive marketplace and intolerance of downtime have increased, while maintenance costs have risen. Along with the demands for greater reliability, a new awareness of failure processes, improved management techniques and new technologies allowed for a broader understanding of machine and component health. The understanding of risk has become essential. Environmental and safety issues are paramount. New concepts like condition monitoring, just-in-time manufacturing, quality standards, expert systems, and reliability-centered maintenance have also emerged on the scene.
Maintenance programs of today
Advanced Technology Servicesconducted a survey through a third-party source to collect data about current maintenance practices at approximately 200 manufacturing facilities. Below we list the findings – producing a snapshot of what today’s typical maintenance program looks like.
Maintenance strategies:88% of manufacturing facilities follow a preventive maintenance strategy; 52% have implemented a computerized maintenance management system (CMMS), and 51% use a run-to-failure method.
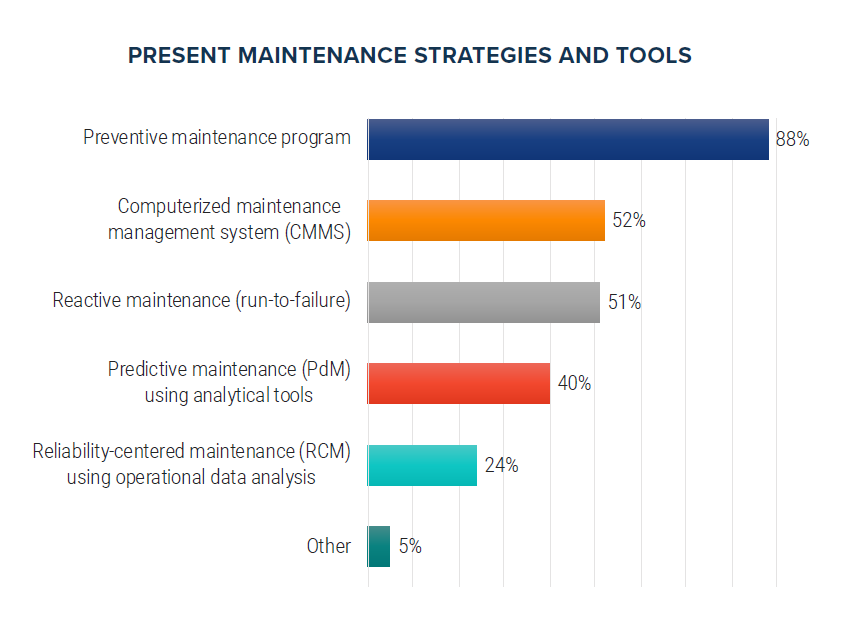
注意系统:Production equipment, rotating equipment (motors, power transmission, etc.), and fluid power systems (air, hydraulic, etc.) are the three areas where facilities dedicate the most maintenance support. Other areas of significant maintenance support are internal electrical distribution systems and material handling equipment.
Plans to decrease downtime:The study’s respondents reveal a variety of plans being made to reduce unscheduled downtime at their plants. 56% percent say the plants plan to upgrade their equipment; 47% plan to improve and/or increase the frequency of training; 45% intend to evolve to a PdM strategy; and 38% expect to increase their asset monitoring capabilities.
Technologies:The most common technologies facilities use to monitor/manage maintenance are CMMS (54%), in-house spreadsheets/schedules (49%), and automated maintenance schedules (44%).
Outsourcing:The study found that 88% plan to outsource some or all of their industrial maintenance operations. Among the leading causes are lack of skills among current staff and lack of time and resources for maintenance.
What the future looks like
未来的维护系统将实现see greater integration of business and technical systems, with more intelligent use of collected data. They will protect users against change of personnel, with the inherent loss of their learning, and allow better-informed choices for decision-makers. The use of such wide-ranging systems and sensors will allow for vast data collection, which will inevitably causechallenges with data management. This will require exceptionally trained people to run, maintain, and manage these systems and data, which may continue to be a problem if there is a lack of technical talent available. The capture of those with this specialized knowledge and the training of new people will continue to be essential for the exploitation of advanced maintenance.
Throughout the history of maintenance, it has always had the same definition. It is the management, control, and execution which will ensure that design levels of availability and performance of assets are achieved in order to meet the business objectives. The issue that is driving the evolution of maintenance is that the business objectives are variable over time. They have continually changed and will continue well into the future. Only by understanding the underlying issues driving this change will we be better suited to speculate on the future of the maintenance industry. To download the 2021 state of industrial maintenance report, clickhere.